Porte aperte alla stampa stamattina nello stabilimento Amazon di San Salvo. L’appuntamento è stato organizzato dalla multinazionale dell’e-commerce per sottolineare le innovazioni tecnologiche introdotte che rendono il sito sansalvese – che oggi conta circa 460 dipendenti – uno dei più avanzati in Europa e il primo in Italia dotato di particolari impianti.
Gli aspetti più significativi sono stati illustrati da Francesco Raveggi (EHS Director – EU FC and Emerging Markets Amazon) e Gianpiero Negri (EU Senior Manager, Machine Safety – Robotics Advanced Technology Amazon).
Innanzitutto, la filosofia Kaizen, già ben conosciuta da queste parti grazie alla Pilkington: coinvolgere i dipendenti nel miglioramento dei processi e degli aspetti relativi alla sicurezza. «Il dipendente è il miglior ingegnere del proprio posto di lavoro» ha sottolineato Raveggi. Grandi schermi all’ingresso dell’area lavorativa del piano terra riportano i suggerimenti dei lavoratori e lo stato di avanzamento delle migliorie. Personale addetto si occupa a tempo pieno di dare un riscontro agli autori dei consigli entro 24 ore: se è possibile adottarli, a che punto si trova l’implementazione e, se non è possibile, spiegarne il motivo e ringraziarli. L’andamento dell’efficienza è costantemente monitorato e un report settimanale indica se ci sono stati avanzamenti o cali.
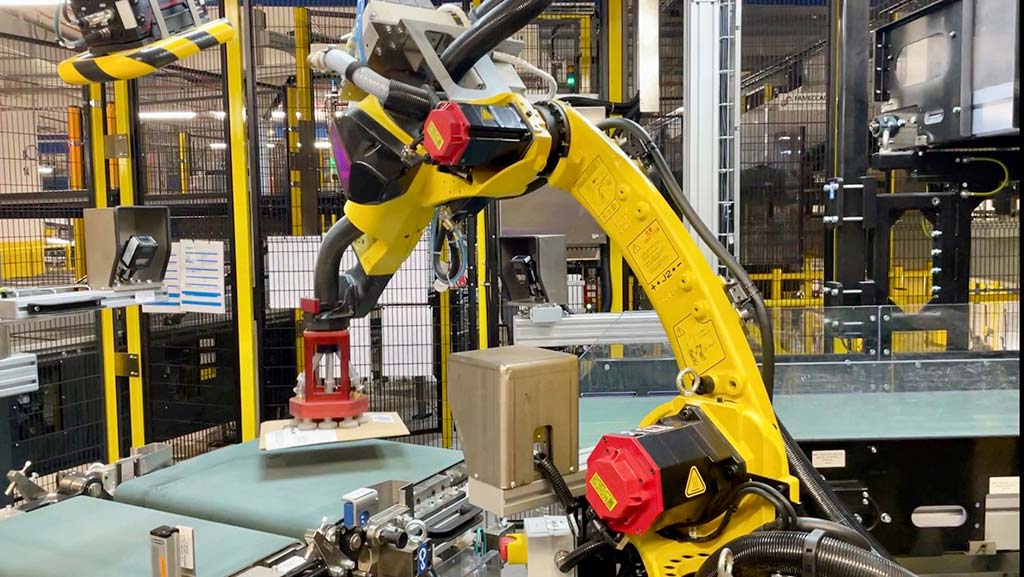
Negli ultimi tre anni, Amazon ha investito 400 milioni di euro nel campo dell’innovazione e dalla partnership tra Innovation Lab e aziende specializzate (tra le quali alcune italiane) sono state introdotti impianti in grado di diminuire lo sforzo fisico e le azioni ripetitive.
Alcuni esempi sono il pallettizzatore e il depallettizzatore: robot che caricano o scaricano (a seconda delle merci in ingresso o uscita) le merci dai pallett evitando l’intervento umano e potenziali infortuni. C’è poi il sistema Fsri che convoglia gli articoli su nastri trasportatori fino alle postazioni dei singoli addetti all’impacchettamento. Quest’ultimo robot è stato sviluppato insieme alla Fameccanica di San Giovanni Teatino. Un altro braccio robotico con terminali a ventosa, nell’area di arrivo delle merci, aiuta a sollevare i pacchi e a depositarli sui nastri trasportatori, «la politica aziendale prevede che i lavoratori non debbano sollevare pesi superiori a 15 chili». In quest’area è possibile osservare anche una miglioria introdotta grazie ai lavoratori: banchi il cui piano di lavoro è dotato di sfere che permettono di far scorrere i pacchi con il minimo sforzo.
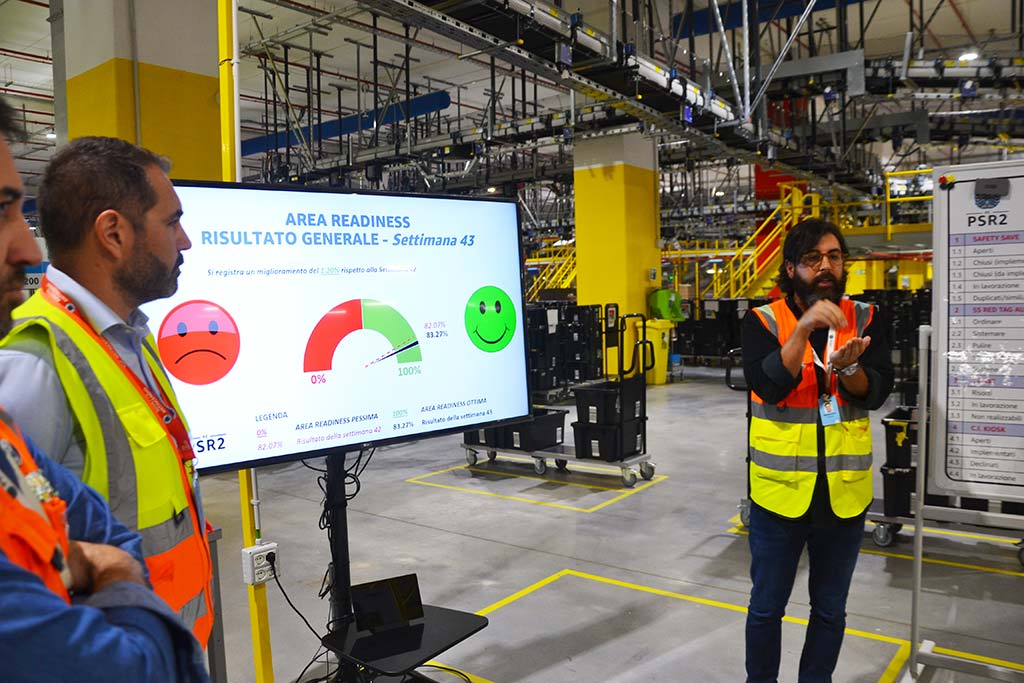
Infine, i tre piani superiori, dove vengono immagazzinate le merci: qui la gran parte della superficie è occupata da scaffali (decine di migliaia complessivamente) contenenti i prodotti che si muovono autonomamente, grazie a carrelli robotici, per raggiungere le postazioni dei lavoratori che vi inseriscono gli articoli. Rispetto al giorno dell’inaugurazione, oggi, l’area è completamente in movimento. Qui gli unici dipendenti che possono accedere sono i manutentori in caso di blocchi: tramite Kindle, si stabilisce un percorso tra gli scaffali che, si fermeranno o rallenteranno al passaggio del lavoratore.
Il rigore delle norme di sicurezza per alcuni versi può apparire eccessivo (la percentuale del monitoraggio, esempi estremi, è influenzata anche dalla presenza di un fazzoletto a terra o di una scopa fuori posto), ma Raveggi è sicuro: «Solo così si raggiunge un alto livello di sicurezza».
Comments 2