Settantacinque dipendenti tra diretti e indiretti, oltre 560 milioni di pezzi prodotti ogni anno e due milioni e mezzo di euro di investimenti negli ultimi tre anni per fare dello stabilimento vastese il centro della produzione. Sono i numero della Bormioli Pharma di Punta Penna che oggi ha aperto le porte alla stampa con Oscar Andreoli (direttore di stabilimento) e Claudia Monfredini (Group Environmental, Sustainability & ESG Manager) per fare un bilancio dell’attività da quando la società parmense si è insediata a Vasto dopo aver rilevato lo stabilimento dalla Guala Closures nel 2020.
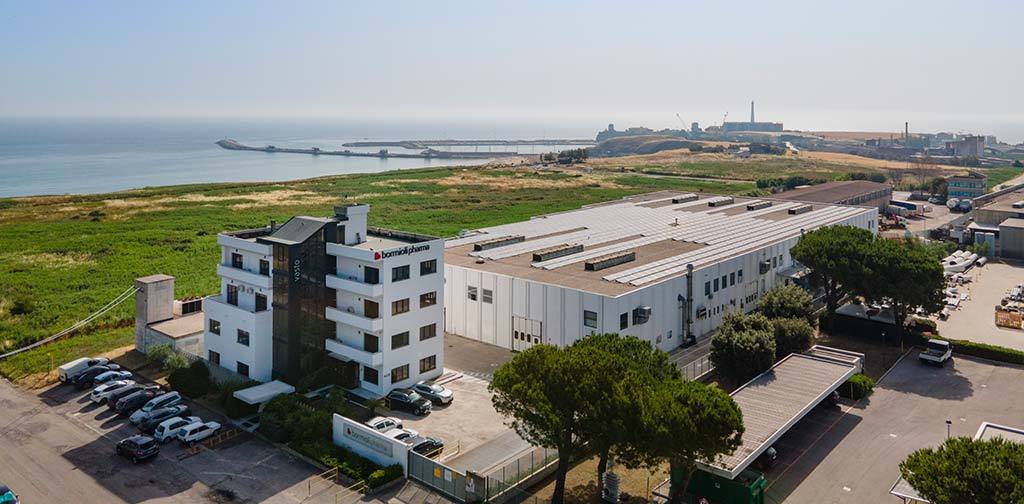
Qui vengono realizzati, per le principali case farmaceutiche, chiusure in gomma e ghiere in alluminio per farmaci iniettabili, la parte in gomma dei contagocce ecc. grazie a una serie di lavorazioni che includono stampaggio, vulcanizzazione, lavaggio e ispezione visiva, e – per le ghiere in alluminio – imbutitura, stampaggio e assemblaggio. Durante la pandemia nello stabilimento sono stati prodotti i tappi in gomma del vaccino russo Sputnik.
Da qualche tempo per rispondere alle numerose commesse, il numero dei lavoratori è stato incrementato e si lavora su tre turni. Dati questi che testimoniano l’importanza del sito vastese nel gruppo (che ha ottenuto le certificazioni di qualità standard ISO 9001 e ISO 15378 applicato al packaging), circostanza evidenziata anche da Andreoli: «Puntiamo a far diventare Vasto il polo produttivo del gruppo, quindi non solo rubber stopper, ma anche nuove linee con altri articoli ormai qui già da un anno e ci sono diverse idee di sviluppo». Le nuove linee citate sono state installate nel mese di gennaio portandone il numero complessivo a 33.
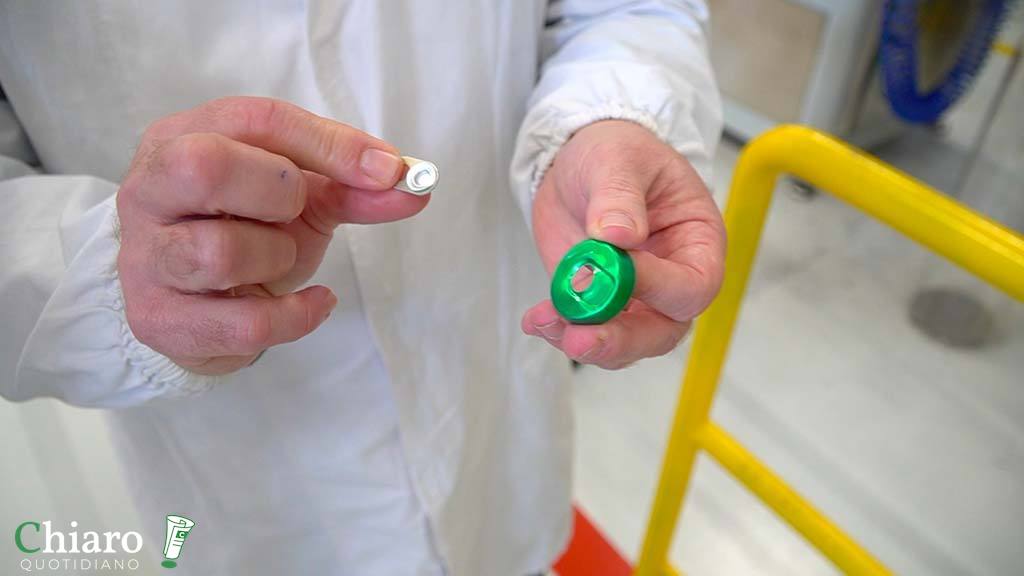
Essendo pezzi che entreranno a contatto con i farmaci ci sono esigenze di massima sterilizzazione e controllo della presenza di difetti e di materiali estranei. Per questo tra le ultime implementazioni ci sono anche l’upgrade tecnologico della camera bianca e l’aggiornamento di tutti i sistemi di visione con telecamere in alta definizione in grado di rilevare micro-difetti nei prodotti finali. All’interno dello stabilimento è presente inoltre un laboratorio per il controllo dei materiali e per la verifica del rispetto delle specifiche di accettazione: «Questo ci consente di eseguire diverse attività di sviluppo, come la creazione di mescole sempre più performanti e adeguate al settore farmaceutico. Fondamentale è inoltre il dialogo con i clienti per un prodotto finale sempre più adatto alle loro esigenze».
Quello di Vasto è lo stabilimento più a Sud del gruppo, da qui i prodotti partono su gomma principalmente per la sede di Parma, da dove poi raggiungeranno, insieme ai contenitori di vetro, le aziende farmaceutiche di tutto il mondo.
Nei 2,5 milioni di investimento sono stati inoltre implementati anche sistemi per una maggiore sostenibilità dello stabilimento come sistemi di filtraggio e tecnologie per il risparmio della risorsa idrica (fondamentale perché usata per il lavaggio finale dei pezzi e, soprattutto d’estate, il flusso non può interrompersi), l’efficientamento energetico della sala compressori, la realizzazione di chiusure in alluminio flip-off con polimeri provenienti da riciclo post-consumo e l’implementazione di sessioni di formazione rivolte ai dipendenti per sensibilizzarli sulle tematiche di sostenibilità ambientale e sociale.